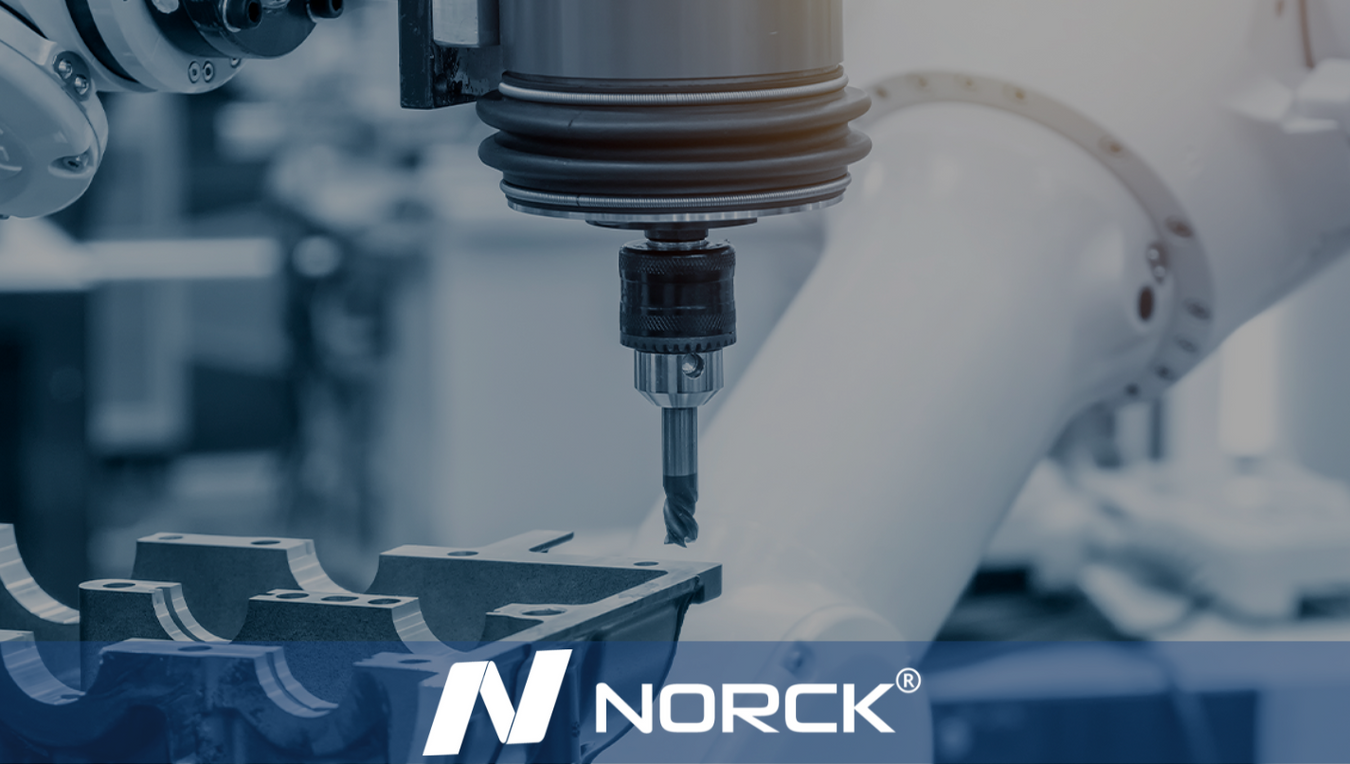
Precision Component Manufacturing with CNC Machining
Unlock the vast mount of CNC machining capacity with Norck for custom component manufacturing, precision metal and plastic manufacturing.
Norck: Your Partner for Precision Production Tooling & High-Volume Injection Molding
Norck delivers expert production tooling solutions, empowering manufacturers across diverse industries to achieve high-quality, cost-effective injection molded parts at scale.
Capabilities for Production Tooling Success:
Norck's Engineering Edge: It's About Reliable Results
Why Choose Norck for Production Tooling?
There are mainly three toolings used for injection molding projects: prototype, bridge, and production tooling.
Production tooling is used for a high-volume injection molding process to mass produce a part or product. Its mold is made from rigid steel and contains a cooling system, which makes its cost higher than bridge or prototype tooling. Its material is heat treated to withstand up to a million shots.
Production tooling offers many advantages:
• Higher volume: Production toolings can produce a high volume of a part or assembly depending on their complexity.
• Repeatability: A significant number of manufactured parts will conform to specifications. And defects can be as low as 3.4 per million parts.
• Rapid fabrication process: The fabrication process time is cut short due to the simplicity of the process.
• Low production costs: The production cost is reduced due to the large number of produced parts which will decrease the cost per part.
But there are some disadvantages as well:
- Higher tooling cost: Production tooling cost is higher than prototype and bridge tooling due to the used material, treatment, and extra features such as a cooling system.
- Long development time of tooling: Due to the complexity of the mold, the development time might be longer, thus the need for bridge tooling.
The production injection molding process is made through four steps:
1. Plastification: The plastic granules are transferred from the hopper to the mold using a rotating screw and molted using heaters.
2. Injection: The screw will advance to increase pressure in the injection chamber to inject the molted plastic into the mold. The two cavities are maintained close until the plastic solidifies
3. Cooling: After injection, the molted plastic will be cooled down to become solid using a cooling circuit. The screw will hold its position to hold the pressure inside the mold.
4. Ejection: After the molted plastic solidifies using a cooling circuit, the Die is opened, and the part is ejected via ejector pins. The screws will retreat to prepare for the next injection.
Obtaining a fully functional part might require extra processing for features that can’t be made with the Production tooling process, such as taping. The designed part should follow Production tooling design guidelines.
Norck is a technology-powered manufacturing leader specializing in CNC machining, 3D printing, sheet metal fabrication, and injection molding. Our intelligent, data-driven approach ensures exceptional quality, optimized costs, and seamless supply chain management for companies worldwide.
Key Services:
Why Choose Norck?
Experience the Norck difference. Get a quote fast for your manufacturing needs today!
Unlock the vast mount of CNC machining capacity with Norck for custom component manufacturing, precision metal and plastic manufacturing.
Whether you need 3D-printed parts in plastic or metal, Norck has the right capacity and solution for you.
Thousands of companies around the world rely on Norck's vast capacity and its extremely qualified capabilities to get their sheet metals fabricated.
Norck's advanced CNC machining capabilities include precision turning, milling, grinding, and honing.
Norck provides precision CNC cutting services such as laser cutting, plasma cutting, and waterjet cutting.
Norck's on-demand 3D printing and additive manufacturing services include nearly all 3D printing methods and technologies.
Norck's advanced technical and technological capabilities make it one of the most on-demand sheet metal fabrication companies across the world.
Looking for a reliable, lifelong supplier to manufacture your next custom metal parts? Click to learn more about Norck’s capabilities in On Demand CNC machining.
All industries including consumer products, electronics, energy, hardware, aerospace, defense, automotive, robotics, machinery are covered.
In a hurry to test before embarking on a full scale production or need high volume production? Turn to Norck for its advanced 3D printing and rapid prototyping services for your next project.
Get a quote for your next sheet metal part, custom part made with CNC machining, or 3D printing.