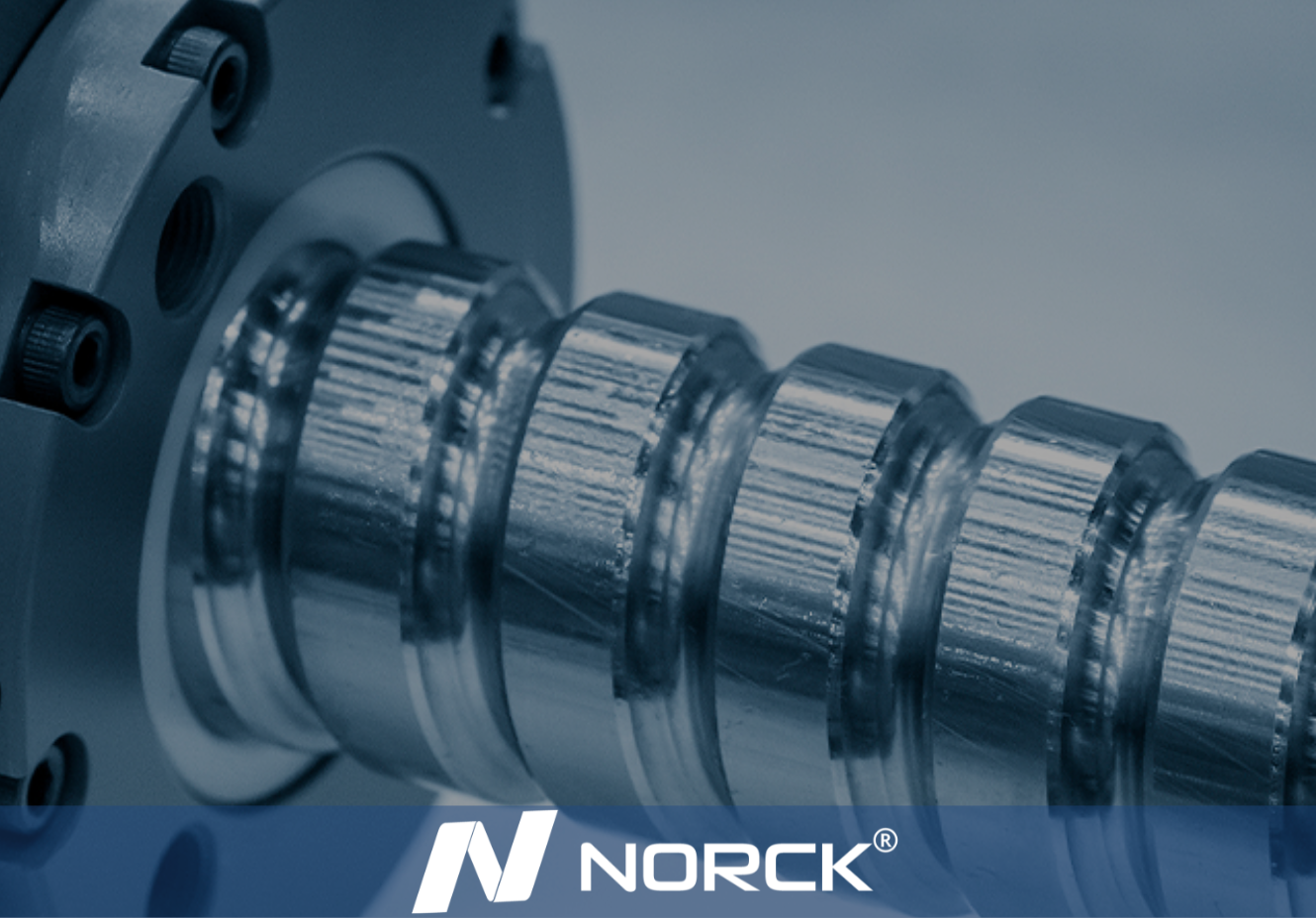
Precision CNC Machining
Norck's advanced CNC machining capabilities include precision turning, milling, grinding, and honing.
Norck: Precision Edge Bending for Your Sheet Metal Needs
Norck delivers expertly formed sheet metal components using precision edge bending techniques. We specialize in aerospace, defense, robotics, industrial, automotive, electronics, energy, hardware, and consumer product applications where accurate bends, complex profiles, and custom sheet metal solutions are required.
Capabilities for Edge Bending Excellence:
Norck's Engineering Edge: It's More Than Just a Bend
Why Choose Norck for Edge Bending?
Sheet metal edge bending, also known as flange forming, is a process that involves applying force to an edge of a metal sheet to cause it to bend along a straight axis. It involves using a punch and die tool designed to create a bend along the edge of a sheet metal part.
Edge bending is mainly used in sheet metal fabrication to create flanges along an edge of sheet metal parts Flanges can be used for attaching other components, adding strength to a part, or for aesthetic or functional reasons.
Sheet metal components are used in:
• Construction: Bending components for construction projects such as roofing and siding
• Automotive: Bending sheet metal for use in body parts such as doors, hoods, and fenders
• Aerospace: Bending sheet metal for use in the manufacturing of fuselage, doors, and fenders
• Advertising: Bending sheet metal for signage and advertising, including signs and billboards
• Food processing: Bending sheet metal for beverages, kitchen equipment
• Transportation: Bending sheet metal parts for cars, trains, buses, and aircraft
• Art: Bending sheet metal for use in building cladding
Edge bending consists of transforming an edge of sheet metal into an angle. It is fixed between two die parts, and the free edge is punched to form
the desired shape.
Loading the sheet metal: The sheet metal is placed into the press brake machine, ensuring that the edge that needs to be bent is appropriately aligned with the punch and die tool. The alignment is crucial to ensure the accuracy and precision of the bend. The sheet metal is secured using clamps or other holding devices to prevent movement or shifting during bending.
Holding the sheet metal in place: The upper die is lowered to clamp the metal sheet securely between the two dies, holding it in place while the punch applies force to the sheet. The clamping force created by the upper die helps to keep the metal sheet stable during the bending process, ensuring that the bend is formed consistently and accurately
Edge bending the workpiece: The punch is lowered towards the metal sheet using a press brake machine. Which applies a force to the sheet metal. As the punch presses into the sheet metal, the force causes the sheet metal to deform and take on the shape of the punch, creating a bend at the desired angle.
Unloading: Once the bending process is completed, the workpiece is removed from the die of the press brake machine. After the inspection, the workpiece can be moved to the next step in the manufacturing process, such as welding, finishing, or assembly.
Norck is a technology-powered manufacturing leader specializing in CNC machining, 3D printing, sheet metal fabrication, and injection molding. Our intelligent, data-driven approach ensures exceptional quality, optimized costs, and seamless supply chain management for companies worldwide.
Key Services:
Why Choose Norck?
Experience the Norck difference. Get a quote fast for your manufacturing needs today!
Norck's advanced CNC machining capabilities include precision turning, milling, grinding, and honing.
Norck provides precision CNC cutting services such as laser cutting, plasma cutting, and waterjet cutting.
Norck's on-demand 3D printing and additive manufacturing services include nearly all 3D printing methods and technologies.
Norck's advanced technical and technological capabilities make it one of the most on-demand sheet metal fabrication companies across the world.
Unlock the vast mount of CNC machining capacity with Norck for custom component manufacturing, precision metal and plastic manufacturing.
Whether you need 3D-printed parts in plastic or metal, Norck has the right capacity and solution for you.
Thousands of companies around the world rely on Norck's vast capacity and its extremely qualified capabilities to get their sheet metals fabricated.
Looking for a reliable, lifelong supplier to manufacture your next custom metal parts? Click to learn more about Norck’s capabilities in On Demand CNC machining.
All industries including consumer products, electronics, energy, hardware, aerospace, defense, automotive, robotics, machinery are covered.
In a hurry to test before embarking on a full scale production or need high volume production? Turn to Norck for its advanced 3D printing and rapid prototyping services for your next project.
Get a quote for your next sheet metal part, custom part made with CNC machining, or 3D printing.